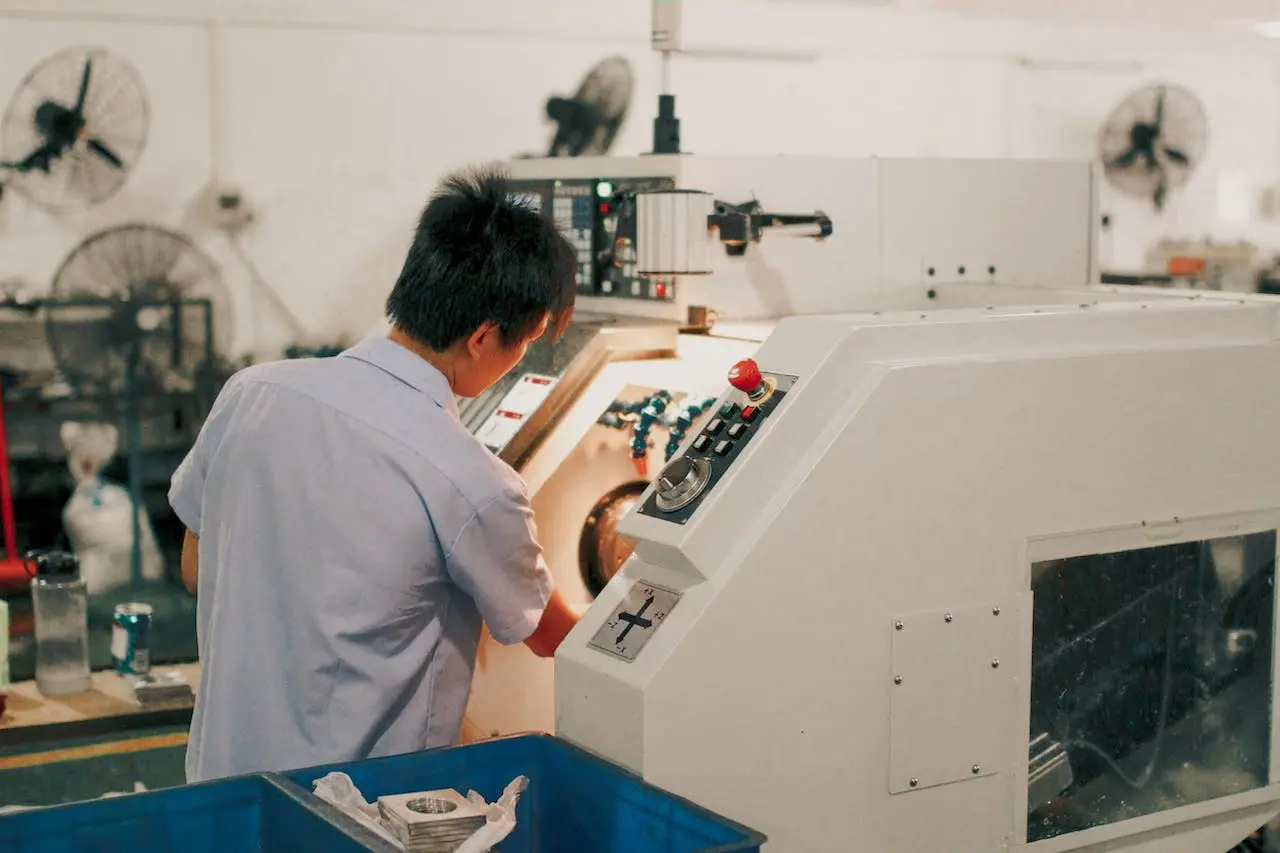
Selecting the right PLC programmer for your automation project is crucial to ensure efficient implementation and ongoing operations. With the right expertise, a PLC programmer analyzes your requirements, recommends optimal solutions, develops reliable PLC code, and provides ongoing support.
This guide covers key factors when choosing your PLC programming resource.
How to Choose the Right PLC
The controller forms the backbone of any automated system, so choosing the right PLC is an essential first step. Consider I/O requirements, speed and cycle times, memory needs, communication protocols, and hardware specifications. A programmer can help match a PLC to your application requirements and budget. Opt for recognized brands offering strong technical support and local parts availability.
Understanding the Basics: What is a PLC and How Does it Work?
A PLC is an industrial computer that manages automation systems in real-time. They process inputs from sensors and output commands to actuators like motors, valves, switches, and more based on the logic, sequencing, timing, counting and computing functions programmed into them. PLCs offer reliable performance for controlling industrial machines and processes. They are more flexible, scalable and cost-effective than relying solely on physical control systems made up of timers, relays and other devices.
Identifying Your Application Requirements: Factors to Consider Before Choosing a PLC
Defining your specific automation requirements is vital for identifying the optimal PLC solution. Consider factors like:
- Inputs/Outputs: Determine the number and types of field devices the PLC system will interface with. Complex systems require more I/O.
- Environment/Location: Will the PLC be utilized indoors or outdoors? Extreme temperatures, dust, moisture and corrosive fumes can impact the models chosen.
- Power: Ascertain available power sources and backup requirements. Some PLCs offer battery or solar options.
- Communication Protocols: Networking and data exchange protocols like EtherNet/IP and PROFINET should match your infrastructure.
- Data Processing Needs: Assess scanning speeds, logic requirements and memory needs early on when selecting PLC hardware.
- Certifications: For hazardous locations, specialized PLCs meet standards like UL, FM, ATEX, IECEx, NEMA, CSA and others.
- Future Expansion: Consider the likelihood of upgrading I/O counts, data storage, communications and other PLC elements later on.
Types of PLCs: Which is the Best Fit for Your Project?
PLCs are available in various configurations to suit diverse automation needs:
- Nano PLCs offer compact, economical solutions for small I/O count applications.
- Micro PLCs balance costs and capabilities for low to moderately complex systems.
- Modular PLCs allow flexible expansion – connect additional I/O modules as needs grow.
- Rackmounts offer advanced capabilities required in complex, high-I/O automation systems commonly seen in automotive, chemical and other industrial settings.
Select PLC types pairing sufficient capabilities with affordability and ease of use based on scale and complexity of application.
Key Features to Look for in a PLC: Essential Functions and Capabilities
- I/O: Sufficient input/output ports for interfacing with devices matching needed types and counts
- Processing speed: Scan rates, logic solving speeds aligning with time-critical system demands
- Programming methods: Support (ladder logic, instruction list, C) fitting programmer preferences
- Simulation/testing: Tools for simulating real-world operating conditions before live deployment
- Communication: Required network/bus connectivity (EtherNet/IP, PROFINET etc) and protocols
- HMI compatibility: Ability to interface modern HMIs (human-machine interfaces) for viewing data and issuing commands
- Data handling: Memory, logging and trace features per analytics needs
- Certifications: Meet safety and environmental standards for industry and location
Programming Considerations: Ease of Use and Compatibility with Existing Systems
Ideally, PLCs should integrate easily with existing automation infrastructure (SCADA etc). Ensure chosen PLCs can be programmed efficiently within the constraints of particular applications.
- International Standards like IEC 61131-3 help ensure the portability and interoperability of PLC programs between hardware platforms.
- Ladder logic remains the most popular PLC programming language globally due to its graphical nature and resemblance to electromechanical relay circuits.
- Modern high-level languages (C, BASIC, Pascal) simplify coding complex data processing features.
- Ensure programming software provides troubleshooting features like simulation and debugging to save commissioning time.
- Remote monitoring/editing capabilities facilitate fast diagnosis and program corrections by suppliers.
- Code libraries/reuse speed up and simplify programming for repetitive or common tasks.
Maintenance and Support: Ensuring Long-Term Reliability and Efficiency
Ongoing PLC maintenance and support needs factoring:
- Parts availability: 10-20 year lifecycles typical for name-brand PLCs – ensure spare parts remain consistently available.
- Training: Equipment user training is essential for proper operation and troubleshooting.
- Manuals: Thorough documentation accelerates learning and diagnoses issues.
- Updates: Regular PLC firmware/software updates are necessary for optimizing performance and fixing bugs when available.
- Support: Programming backup assistance quickly resolves errors not fixable in-house.
- Lifecycle policies: Understand manufacturer timelines for guaranteed product serviceability – repairs, software support etc.
Cost Considerations: Balancing Budget and Performance
Upfront PLC costs constitute only about 5-10% of overall lifecycle expenses on automation systems with programming, installation, maintenance and downtime impacts making up the lion’s share. Avoid false economies – balance capabilities against budgets.
- Hardware: Price PLC central processing unit, I/O cards, accessories like memory cards and cables
- Software: Programming packages, HMI/SCADA licenses add to costs
- Services: Programming, and commissioning help offset internal resource constraints
- Training: Equipment user education protects investments via proper operation and maintenance
- Downtime: Capable PLCs with strong support help maximize production system availability
Choosing the Right Supplier
Select PLC programmers investing time to understand application requirements and constraints. Domain expertise and communication skills should complement technical competencies. Additional criteria include:
- Experience: Proven track record completing similar automation projects
- Standards: Compliance with ISO 9001 or other internationally recognized quality standards
- Support: Ability to quickly troubleshoot and debug PLC programs remotely if needed
- Training: Capability to educate equipment operators to leverage PLCs fully and properly
- Partnerships: Strong working relationships with major PLC hardware vendors
- Location: Service engineers are readily accessible for on-site support as necessary
Final Thoughts
In summary, organizations must carefully balance PLC capabilities, ease of support, and lifecycle costs when selecting the right programmable logic controller. Defining your requirements ahead of time and choosing PLC programmers with specialized domain expertise gives automation projects the best chance of ongoing success through maximized ROI.
While upfront price matters, it makes up just a small fraction of the overall expense of a PLC system over years of utilization. Partnering with the right PLC programmer provides vital guidance during product selection while streamlining commissioning, operation and maintenance for the automation lifecycle.